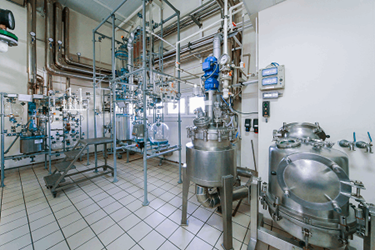
Pharma 4.0 is an all-inclusive term for a broad range of technologies and approaches, including devices and connected sensors that make up Big Data, the Internet of Things, and advanced analytics approaches, along with new digitally enabled bio/pharma manufacturing techniques. All of those advances have potential applications in Maintenance 4.0. Maintenance 4.0 does not arrive at your facility’s doorstep, however; it needs to be planned, organized, and executed. This article is about how to mature the maintenance department and its stakeholders toward Maintenance 4.0.
In bio/pharma operations, safe operation is the paramount prerequisite, as it is in any manufacturing organization nowadays. However, “license to operate” is the second most important requirement, and maintenance is one of the essential foundational pillars of such license to operate. Once equipment is released for GMP use, maintenance assures ongoing compliance between campaigns or sequences of batches, and it is the activity that keeps the performance of an asset within the limits of the original design specifications. For the latter, the preferred technique is centerlining.
Maintenance’s value comes through applied knowledge, derived from information, which comes out of organized data. Modern maintenance organizations have a mixture of preventive, predictive, and some degree of corrective maintenance, typically risk-based, with a low-risk or high-reliability profile. Maintenance 4.0 is the output of a reversed flow: value-added data converts into valuable information that delivers understanding, which allows effective maintenance decisions to run an efficient operation.
Just applying technology in a vacuum and expecting good results doesn’t fly. A Maintenance 4.0 transformation needs to blend traditional improvements with new tools and techniques, and they need to work hand in hand. Real benefits will not materialize by equipping the maintenance groups with virtual/augmented reality technologies without the fundamentals, such as, for example, a robust process for planning and scheduling maintenance activities, already in place.
Who Is Responsible For Maintenance 4.0?
Without discounting the importance of enabling technologies, senior management should consider the fact that change management is integral to the adoption of Maintenance 4.0. From a practical perspective, internal change champions and early adopters should play a role in gaining plant-level buy-in, communicating quick wins, and engaging key stakeholders across the organization.
Maintenance 4.0 is not a top-down decision. It requires the support and input of plant-level staff and operators who will ultimately be responsible for its implementation. Maintenance serves several different stakeholders, each with their own focus. Generally, these are operations, business, and society. The challenge for the maintenance manager is to balance the interests of society (environment, health & safety), business (spent as a percentage of the total asset value), and operations (uptime, overall equipment effectiveness [OEE]).
Maintenance is at the foundation of system life cycle methodology and very technical in its function. In the chain of events in the equipment system life cycle, maintenance is the connecting dot between campaigns or sequences of batches. Responsibility for maintenance needs to be with a dedicated department manager who does not report into the operations position responsible for manufacturing. The pressure to deliver a predefined schedule and maintain compliance by performing maintenance tasks in a nonrelated manufacturing schedule can easily result in production being favored. In such situations, it is preferable to have equal organizational power and be able to escalate where needed. Alternatively, having a combined schedule for delivering commercial demand and allowing for predefined maintenance tasks necessary to meet full compliance provides an integrated approach to system life cycle management.
Maintenance is the noun; the activity to be performed. However, it is also the process, which means it is a systematic series of actions directed to keep in existence or continuance, and it is a system, which means it is a coordinated body of activities directed to some end. It is a system to plan, organize, and provide care and custody of assets during their life cycles.
The 5 Core Aspects Of Maintenance 4.0
Maintenance 4.0 is composed of five types of activities whose purpose is to keep each asset in a reliable, compliant, and operable state: periodic inspection, prescriptive maintenance, preventive (routine) maintenance, predictive (reliability) maintenance, and corrective/reactive (breakdown) maintenance. These definitions set the blueprint and framework for a complete, comprehensive, and compliant maintenance function in a highly regulated environment. What that looks like is different for almost every company, and so is how it is implemented.
1. Periodic Inspection
Inspections provide the necessary data to know the state of the equipment, which allows us to make choices. Optimizing the time interval between maintenance inspections can minimize the cost of preventive inspections and reactive maintenance. Inspection frequency should be set according to the failure developing period (FDP), by estimating the FDP and setting the inspection frequency to FDP over two. As an example, if we estimate an FDP of four months, we would set the initial inspection frequency at two months. Precise and accurate historical data at the plant is an excellent first indication for FDP.
2. Prescriptive Maintenance
Prescriptive maintenance is the latest level in the evolution of routines in maintenance. In comparison with predictive practices, instead of only predicting a failure, prescriptive maintenance is “prescribing” an outcome-focused behavior for maintenance and operations that is based on prescriptive analytics. It is essential to mention that this type of maintenance is still in its infancy but is likely to become the next best practice in reliability and maintenance. Prescriptive maintenance allows focusing on servicing assets in the most efficient ways possible to increase uptime.
3. Preventive (Routine) Maintenance
Preventive maintenance is taking precautionary and proactive steps against unscheduled equipment downtime and other avoidable failures. Preventive maintenance avoids unexpected breakdowns in the production line.
4. Predictive (Reliability) Maintenance
Predictive maintenance is a condition-based process that forecasts when an equipment failure could occur and provides advanced warning of such. This is realized by monitoring the condition of the equipment and performing maintenance before failure is expected.
Examples of equipment monitoring methods include: vibration analysis, temperature/infrared thermography, noise/acoustic analysis/listening, visual inspection, fluids analysis (oil), pressure differential, and motion sensors.
5. Corrective/Reactive Maintenance
Corrective and reactive maintenance are done so that equipment can perform its intended function. Corrective maintenance is done after a failure is found, while reactive maintenance is done after a breakdown happens. When used, this strategy is recommended only on equipment that does not affect product quality.
The maintenance flow in the picture below is a complete and inclusive process governing all maintenance functions. Maturing toward Maintenance 4.0 does not mean eliminating existing maintenance processes and technologies. Yes, there are legacy systems that are not the most effective, but the default should be to adapt existing practices. Your organization, most likely, already implements certain so-called Maintenance 4.0 practices.

Figure 1 Comprehensive process-flow for maintenance, covered in four procedures: (1) overarching process flow, (2) preventive SOP, (3) corrective SOP, and (4) a shutdown SOP
Preventive maintenance is time-based, predictive maintenance is condition-based, and both have quality-approved work instructions to take equipment out of service, service the unit, qualify the revised equipment, and hand it back to operations. Corrective and reactive maintenance procedures can be covered under the preventive/predictive maintenance procedure for those parts failures that are described in work instructions for preventive/predictive maintenance. For those that are not yet described, work plans need to be drafted and submitted to quality for approval before execution can be performed.
Conclusion Traditionally, maintenance is fixing something that is broken. From fixing what is broken (corrective), maintenance has developed to replacing wearable parts before they fail (preventive), to measuring specific performance indicating potential future failure (predictive), and to timely replacing the wearable part. The next stage in maintenance management (Maintenance 4.0) is to go beyond predictive to the initial stage of an asset — commissioning the assets and deploying the same tools and techniques to set the measures within the design specification from the beginning onward and using indicative measures to keep the asset in its original design specification.
Leave a Reply